Custom Industrial Plasma Systems
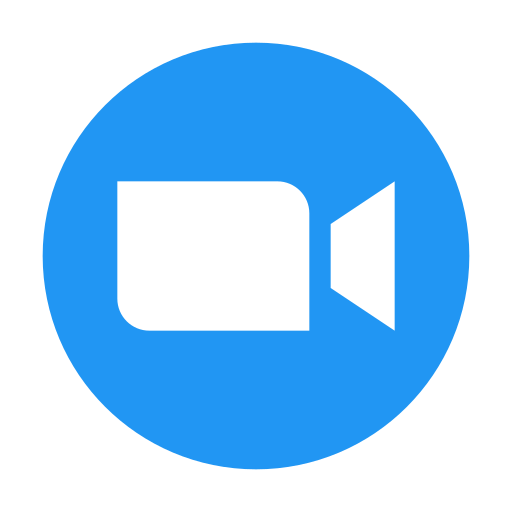
Custom industrial plasma systems are used to enable and improve new or existing product lines. The process of producing a product in volume can have many challenges. Improving quality and reliability with a controlled method of activation, cleaning, etching or coating of parts in volume are the primary advantage of having a custom industrial plasma system.
Request a Low Pressure Plasma QuotationAtmospheric pressure plasma is suitable for a wide range of applications. Primarily, the systems are optimized for high volume plasma treatment of communication device surfaces in manufacturing.
For more than 30 years, we've acquired relevant experience with Industrial Plasma Systems to become a technology leader in the implementation and use of plasma systems.
Request A QuotePlasma cleaning and activation for adhesion optimization in a high volume process with a short takt time is one of the key uses of an industrial plasma system.
Plasma etching or using plasma to reduce an oxide in a high volume manufacturing process is one of the key applications of large scale industrial plasma systems.
Plasma coating a large number of elastomeric seals or O-rings using plasma processing in a high volume manufacturing process is a good application for custom industrial plasma systems.
Another application of plasma coating is parts that require a hydrophobic coating. An example of this is pipet tips for medical or biological experimentation.
Control Cabinet:
W 600 mm H 1700 mm D 800 mm
Chamber:
W 15.8" x H 15.8" x D 24.6"
Chamber Volume:
100
Gas Supply:
Mass flow controllers
Generator:
1 pc. with 40 kHz
(optional: 13.56 MHz or 2.45 GHz)
Control:
PC
Control Cabinet:
W 600 mm H 1700 mm D 800 mm
Chamber Volume:
120
Gas Supply:
Mass flow controllers
Generator:
1 pc. with 40 kHz
(optional: 13.56 MHz or 2.45 GHz)
Control:
PC
Control Cabinet:
W 600 mm H 2100 mm D 800 mm
Chamber:
W 15.8" x H 23.6" x D 24.6"
Chamber Volume:
150
Gas Supply:
Mass flow controllers
Generator:
1 pc. with 40 kHz
(optional: 13.56 MHz or 2.45 GHz)
Control:
PC
Control Cabinet:
W 600 mm H 2100 mm D 800 mm
Chamber Volume:
600
Gas Supply:
Mass flow controllers
Generator:
1 pc. with 40 kHz
(optional: 13.56 MHz or 2.45 GHz)
Control:
PC
Control Cabinet:
W 600 mm H 2100 mm D 800 mm
Chamber Volume:
600
Gas Supply:
Mass flow controllers
Generator:
1 pc. with 40 kHz
(optional: 13.56 MHz or 2.45 GHz)
Control:
PC
Control Cabinet:
W 600 mm H 2100 mm D 800 mm
Chamber Volume:
7000
Gas Supply:
Mass flow controllers
Generator:
1 pc. with 40 kHz
(optional: 13.56 MHz or 2.45 GHz)
Control:
PC
Control Cabinet:
W 600 mm H 2100 mm D 800 mm
Chamber Volume:
12600
Gas Supply:
Mass flow controllers
Generator:
1 pc. with 40 kHz
(optional: 13.56 MHz or 2.45 GHz)
Control:
PC
Plasma: +1 (248) 761 9253
Distribution: +1 (248) 549 8600
Fax: +1 (248) 549 3533
info@thierry-corp.com