Vacuum Chambers
& Systems
In manufacturing there is a need for high altitude testing, drying, or off gassing of materials or similar application where a controlled and repeatable vacuum environment is required. Our product line focuses on a cost effective vacuum chamber of virtually any size that is easy to use and less expensive than conventional tooling. As a result, we offer a flexible chamber system based on aluminum extrusion profiles and customization according to your specific manufacturing requirements.
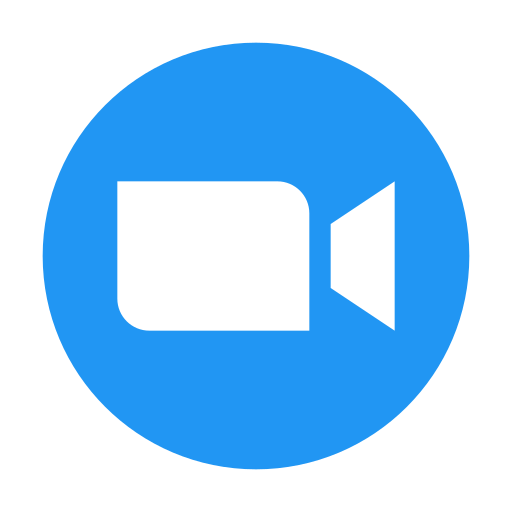