One of the specific purposes of plasma treatments is to plasma coat. There are two ways to plasma coat: plasma-enhanced chemical vapor deposition processes (PECVD) and physical vapor deposition (PVD). PECVD is a chemical vapor deposition (CVD) process that uses cold plasma, and it uses very low deposition temperatures compared to the temperatures used in CVD reactors. PECVD has a wide range of applications; one example is anti-scratch layers in optics. Some advantages of PECVD are its low power source and uniformity of deposited layers. Furthermore, the layers created by PECVD may be of a better quality when compared to CVD so the likelihood of cracking the deposited layer is much smaller. It is also relatively easy to clean the chamber after the PECVD process. This is important because the thick films that form on the chamber walls can contaminate the substrate surface (if the chamber is not cleaned properly).
PVD processes are used to plasma coat surfaces in order to improve wear and oxidation resistance of the material. Its other purposes include improving hardness and lifespan. Plasma treatments are effective and efficient options to change the properties of a material. Unlike CVD where the deposited material is originally in its gaseous form, the deposited material is in the solid state for PVD. PVD occurs under vacuum conditions and includes four different steps:
- The material to be deposited is excited with plasma, to form a vapor
- A reactive gaseous species is introduced
- The reactive gas forms a compound with the vapor formed
- The compound is deposited onto the substrate
Plasma Treatments Introduction
Plasma is the one of the four states of matter; it is ionized gas with an equal amount of free positive and negative charges. If sufficient energy or temperature is supplied to each state, the state is converted in the following order: solid, liquid, gas, and plasma. The plasma changes the surface properties of the material because it transfers extra energy and promotes reactions to occur on the surface. Plasma can change the surface properties without altering the bulk properties of the material. The reactions between the material’s surface and the process gas control the result of the plasma treatment. Plasma treatment is used to plasma clean, activate, etch, and coat. Its applications range from activating the surface of textiles to cleaning the surfaces of medical equipment. Plasma treatment is very environmentally friendly and affordable process.
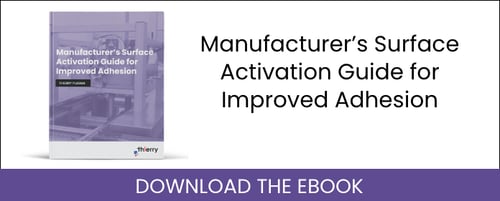